Beryllium Copper Processing Process
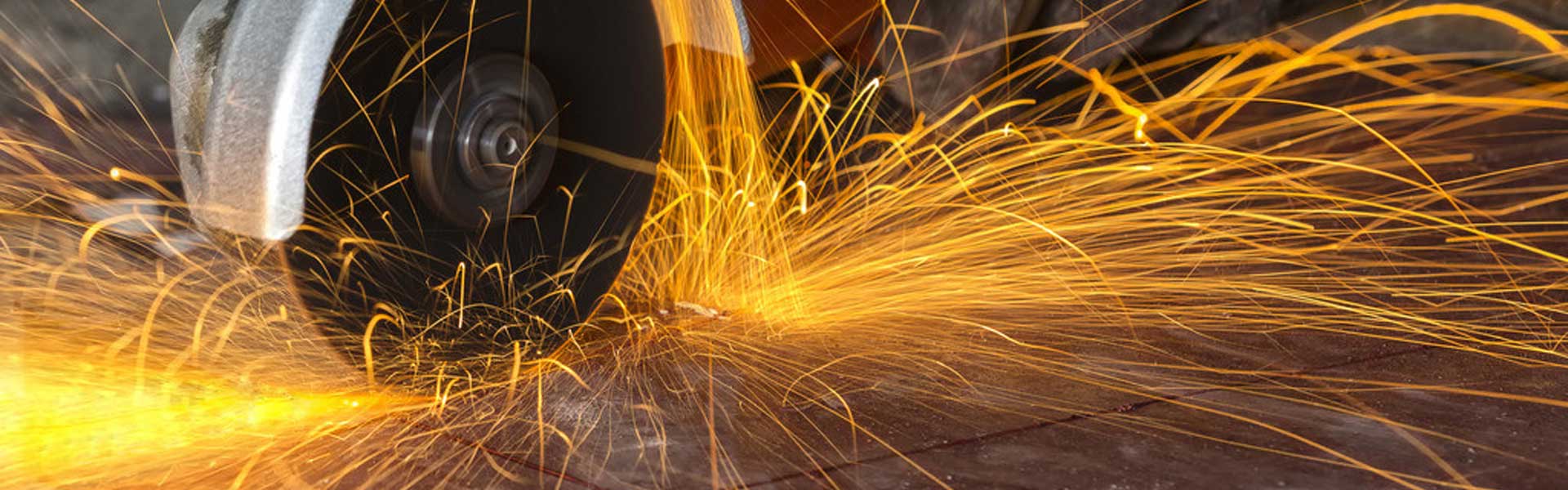
STEP1.Slitting Basic Process
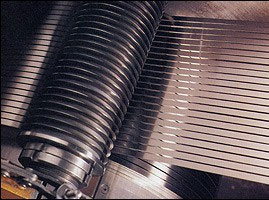
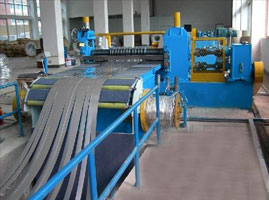
STEP2.Rolling Milling Process
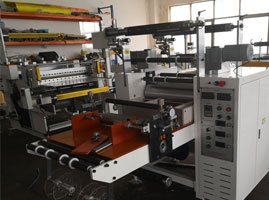
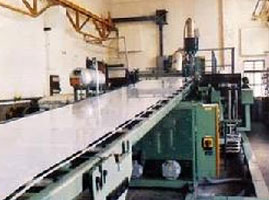
STEP3.Beryllium Copper Electroplating
- 1. Copper plating: used for primer to improve the adhesion and corrosion resistance of the plating layer.
- 2. Nickel plating: used for primer or appearance to improve corrosion resistance and wear resistance (among which chemical nickel is more wear-resistant than chrome plating in modern technology).
- 3. Gold plating: improve conductive contact impedance and enhance signal transmission.
- 4. Palladium nickel plating: improve conductive contact resistance, enhance signal transmission, and have higher wear resistance than gold.
- 5. Tin-lead plating: to improve soldering ability, and soon to be replaced by other substitutes (because the lead is now mostly changed to bright tin and matte tin plating).
Electroplating is a method of laying a layer of metal on a conductor using the principle of electrolysis.
In addition to electrical conductors, electroplating can also be used on specially treated plastics.
- Connect the plated metal to the anode
- The object to be plated is connected to the cathode
- The anode and cathode are connected by an electrolyte solution composed of positive ions of the metal plated
- After the direct current power supply is applied, the anode metal will be oxidized (loss of electrons), and the positive ions in the solution will be reduced at the cathode (get electrons) into atoms and accumulate on the surface of the cathode.
- After electroplating, the aesthetics of the electroplated object is related to the size of the current. The smaller the current, the more beautiful the electroplated object will be; otherwise, some uneven shapes will appear.
- The main purposes of electroplating include preventing metal oxidation (such as rust) and decoration. The outer layer of many coins is also electroplated.
- Sewage produced by electroplating (such as lost electrolyte) is an important source of water pollution. The electroplating process has been widely used in the process of semiconductor and microelectronic component lead frames.
- VCP: Vertical continuous electroplating. The new type of machine currently used on circuit boards has better quality than traditional suspended electroplating.
The coating layer is mostly a single metal or alloy, such as titanium target, zinc, cadmium, gold or brass, bronze, etc.; there are also dispersion layers, such as nickel-silicon carbide, nickel-graphite fluoride, etc.; there are also clad layers, such as steel The copper-nickel-chromium layer, the silver-indium layer on the steel, etc. In addition to iron-based cast iron, steel, and stainless steel, the electroplating matrix materials include non-ferrous metals, or ABS plastic, polypropylene, polysulfone, and phenolic plastics. However, the plastic must undergo special activation and sensitization before electroplating.
In the plating tank containing the electroplating solution, the cleaned and specially pretreated parts to be plated are used as the cathode, and the anode is made of plated metal, and the two poles are respectively connected with the negative and positive electrodes of the DC power supply. The electroplating solution consists of an aqueous solution containing metal-plated compounds, conductive salts, buffers, pH adjusters, additives, and the like. After being energized, the metal ions in the electroplating solution move to the cathode under the action of the potential difference to form a plating layer. The metal of the anode forms metal ions into the electroplating solution to maintain the concentration of metal ions to be plated. In some cases, such as chromium plating, an insoluble anode made of lead and lead-antimony alloy is used, which only serves to transfer electrons and conduct current. The concentration of chromium ions in the electrolyte needs to be maintained by regularly adding chromium compounds to the plating solution. During electroplating, the quality of the anode material, the composition of the electroplating solution, temperature, current density, power-on time, stirring intensity, precipitated impurities, power waveform, etc. will affect the quality of the coating and need to be controlled in a timely manner.
- 1. Cathode: The object to be plated refers to various connector terminals.
- 2. Anode: If it is a soluble anode, it is the metal to be plated. In the case of insoluble anodes, most of them are precious metals (platinum, iridium oxide).
- 3. Electroplating potion: electroplating potion containing metal ions to be plated.
- 4. Electroplating tank: a tank that can withstand and store electroplating solutions, generally considering factors such as strength, corrosion resistance, and temperature resistance.
- 5. Rectifier: A device that provides DC power.
(Grinding → Polishing) → Hanging → Degreasing and degreasing → Washing → (Electrolytic polishing or chemical polishing) → Pickling activation → (Pre-plating) → Electroplating → Washing → (Post-treatment) → Washing → Drying → Hanging down → Inspection package
STEP4.Beryllium Copper Spray Painted
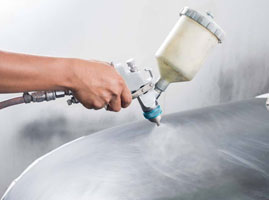
- Capacity: 6-8 tons per day;
- Process Capability:xxxx
- Printable material thickness: 0.05mm-0.5mm
- Printable material width: within 220mm;
- Printing materials involved: white copper, stainless steel, aluminum, copper, tinplate;
- Printing colors involve: yellow, black, white;
- Single-sided and double-sided printing can be performed.
- 1. Dimension detection adopts two-dimensional instrument detection:Refer to customer drawing requirements for testing
- 2. Film thickness detection Use a micrometer to test:The film thickness standard is 8-15UM for OK
- 3. Adhesion test Use a hundred grid knife (10*10 small square) for testing:OK for paint drop area ≤5% (ie ≥4B)
- 4. Bending detection, using impact tester for detection:Bending 90 degrees without paint falling and bursting is OK
- 5. RCA wear resistance test with paper tape wear tester:Abrasion resistance pressure of 175g, 60 laps without leakage, non-conductive is OK
- 6. Insulation test Use insulation tester to test:The insulation value is adjusted to 1000V (4000mΩ) and the test rod is placed on the metal surface and the paint surface is not conductive, then it is OK
- 7. Salt spray test Use salt spray tester to test:Spray continuously for 24 hours, the printing area does not change color, there is no air bubbles, and the paint drop phenomenon is OK
- 8. High temperature test Use high temperature tester to test.Raise the temperature to 260 degrees and bake for 7 minutes without discoloration, it is OK
STEP5.Beryllium Copper Inspection
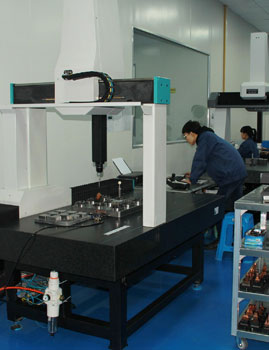
The test force divided by the surface area of the indentation is the Vickers hardness value. Vickers hardness value calculation formula: HV = constant × test force / indentation surface area ≈ 0.1891 F/d2. In the formula: HV-Vickers hardness symbol; F-Test force (in N); d-the arithmetic average of the two diagonals d1 and d2 of the indentation (in mm). In practice, the Vickers hardness value can be obtained by looking up the table according to the diagonal length d. The national standard stipulates that the diagonal length of Vickers hardness indentation ranges from 0.020 to 1.400mm.
Test to determine a series of characteristics of a material under tensile load is also called a tensile test. It is one of the basic methods of material mechanical performance test, mainly used to check whether the material meets the specified standards and study the performance of the material.
- The temperature is 10-35 degrees, and it is not considered room temperature if it exceeds
- The cross-section of the sample or product is not less than 1mm
- The sheet is 0.1-3mm thick and the width is at least 20mm
- The diameter of the cylinder should be greater than 3mm, the length should be at least 250mm, and the diameter of the cylinder should be greater than 10mm.
- Under 80mm, only the tensile strength can be obtained, and the metal wire should be stretched more than 1 meter.
This testing machine uses a high-speed DSP platform with high integration, powerful control, data processing capabilities, and high reliability. It adopts a fully digital, force, deformation, and displacement control system with an adaptive PID algorithm to realize force, deformation, and displacement. Control, each control loop can be automatically switched, and it can control and maintain the rate of test force, deformation, displacement, etc., USB1.1 communication, plug and play interface, this interface can be hot plugged, that is, it has plug and play function . Makes the layout of each interface neat and reasonable, easy to plug and unplug. The system board uses a 4-layer PCB unique anti-interference wiring method, which has strong anti-interference ability. The entire control system has high cost performance and high reliability. The entire test process is controlled by a microcomputer, real-time dynamic Display load value, displacement value, deformation value, test speed and test curve. Using a computer for data processing and analysis, the test results can be automatically saved, the test curve can be recalled after the test, and the test process can be reproduced through curve traversal. The test software under the full Chinese Windows platform has strong data and graphics processing functions , It can print out a complete test report and test curve in real time, with complete limit protection, overload protection, emergency stop and other safety protection functions. The data results that can be obtained: tensile strength, yield point, yield strength, elongation after fracture, Area shrinkage after fracture.
The highest temperature that the main test material can withstand.
An environmental test that mainly uses artificially simulated salt spray environmental conditions created by salt spray test equipment to assess the corrosion resistance of products or metal materials. It is divided into two categories, one is natural environmental exposure test, and the other is artificial accelerated simulated salt spray environmental test. The artificial simulated salt spray environment test is to use a kind of test equipment with a certain volume space-the salt spray test box, and use artificial methods in the volume space to create a salt spray environment to assess the quality of the salt spray corrosion resistance of the product . Compared with the natural environment, the salt concentration of chloride in the salt spray environment can be several or tens of times the salt spray content of the general natural environment, which greatly increases the corrosion speed. The salt spray test is performed on the product and the result is obtained The time is also greatly shortened. For example, if a product sample is tested in a natural exposure environment, it may take 1 year for its corrosion, while the test under artificially simulated salt spray environment conditions requires only 24 hours to obtain similar results.
Learn More About Wonder Copper Inc
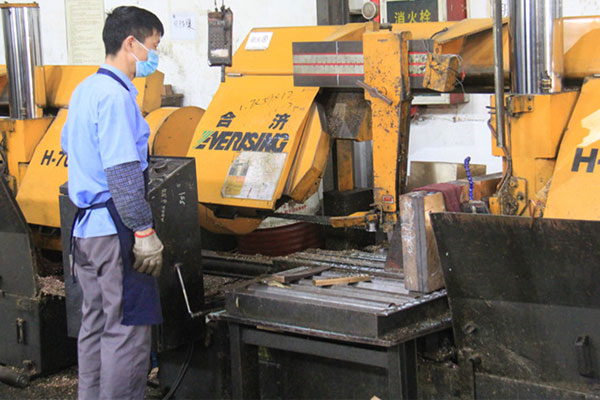
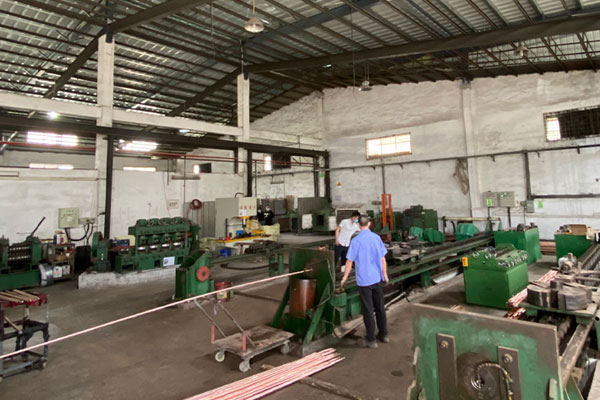
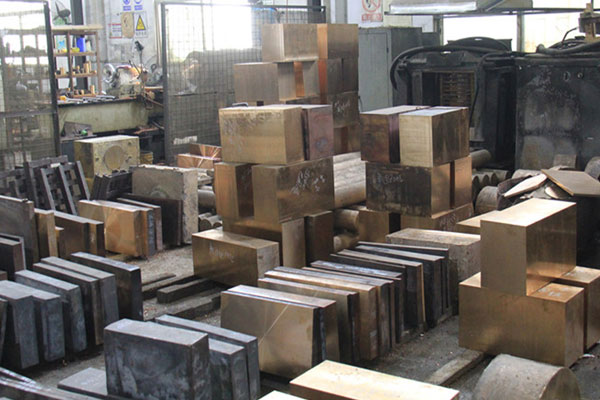

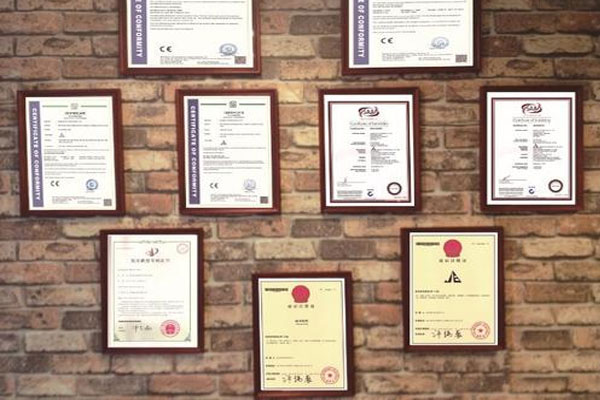
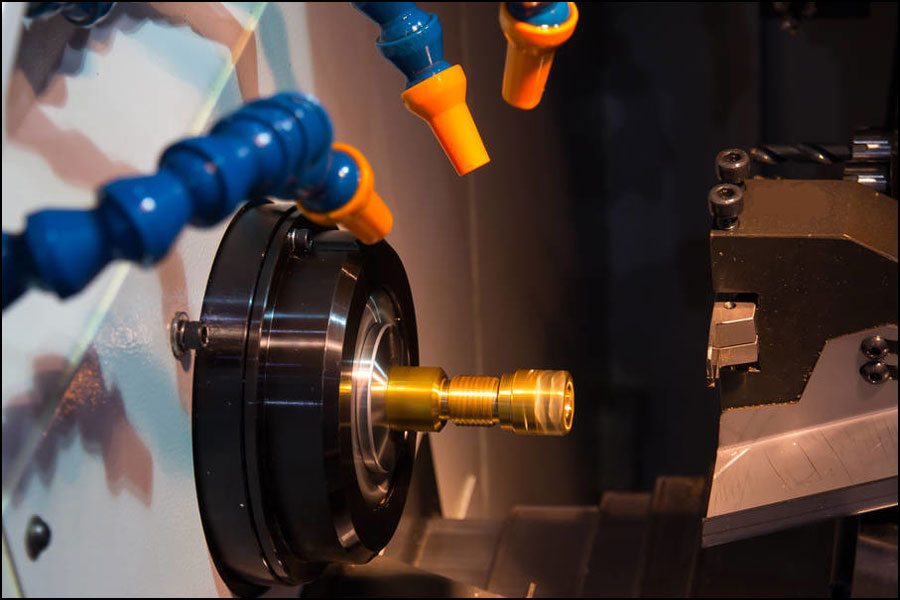